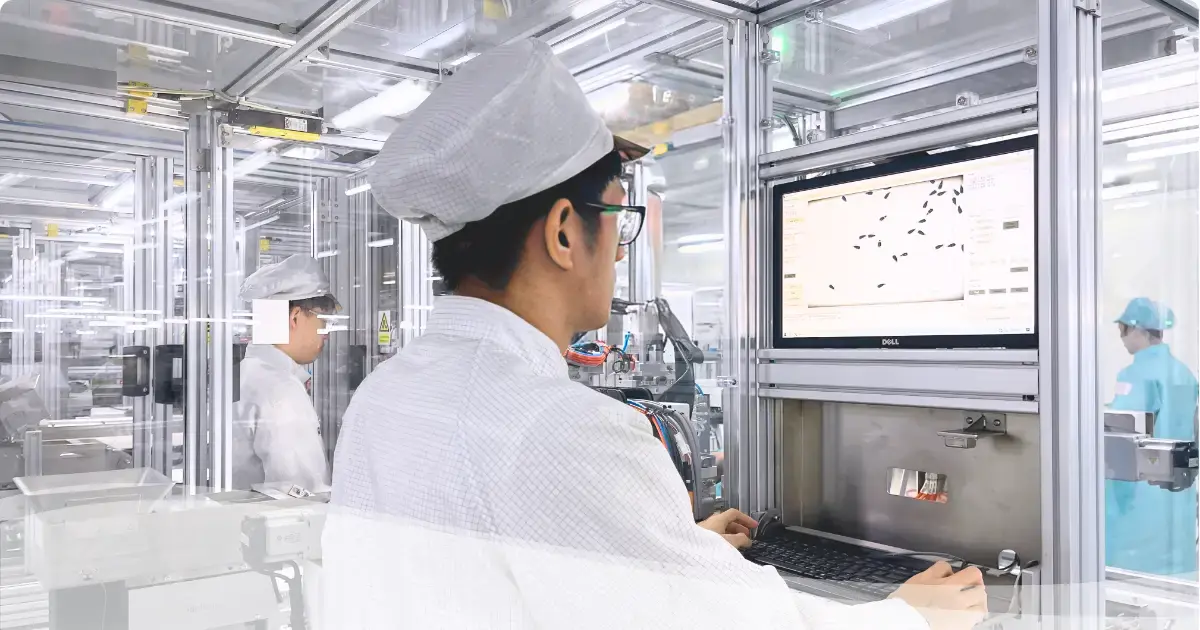
What Is OEE in Electronics Manufacturing and Why It Matters | SVI EMS Insights
More than just a number, Overall Equipment Effectiveness (OEE) is a lens through which world-class EMS providers measure productivity, identify bottlenecks, and implement sustainable improvements that deliver value to customers. It’s also a key part of how SVI builds and maintains a culture of Continuous Improvement (CI).
📊 Understanding OEE: The Three Dimensions of Effectiveness
OEE quantifies how effectively a piece of equipment is used in production by combining three key factors — Availability, Performance, and Quality — into a single percentage:
- Availability: Is the machine running when it’s supposed to?
- Performance: Is it running at its maximum designed speed?
- Quality: Is it producing good parts with minimal defects?
OEE = Availability × Performance × Quality
A perfect OEE score of 100% means equipment is producing only good parts, as fast as possible, with no downtime — an ideal rarely reached, but always pursued.
🏭 Why OEE Matters in EMS
In Electronics Manufacturing Services (EMS) — particularly in high-mix, low-volume environments like ours at SVI — line efficiency isn’t just about uptime. It’s about responding quickly to changeovers, ensuring defect-free output, and maximizing yield per setup.
Monitoring OEE helps us:
- Detect root causes of downtime and slow cycles
- Balance line utilization across shifts and regions
- Reduce rework and material waste
- Make data-driven investments in automation or process changes
Whether it’s an SMT line in Thailand or a box-build line in Slovakia, OEE gives our cross-functional teams a common language for efficiency and improvement.
👉 At SVI, we continuously pursue an OEE benchmark of 85% — in our core manufacturing processes, especially within SMT operations.
🔄 OEE as Part of Our Continuous Improvement Culture
At SVI, OEE is not tracked in isolation. It’s part of a broader Continuous Improvement ecosystem, where daily shopfloor data drives regular CI meetings, root cause analysis, and Kaizen projects.
From implementing Work Cell Kaizen in 2012 to launching our Digital Factory Andromeda in 2023, we’ve evolved how we apply OEE in both manual and automated environments.
📈 The Data Behind the Improvement: Lean Six Sigma and OEE
OEE also plays a critical role in our Lean Six Sigma strategy. It provides the performance data that feeds directly into DMAIC problem-solving, helping our Green and Black Belts uncover patterns, prioritize actions, and validate improvements.
🧠 From Metrics to Mindset
OEE is not just for engineers. At SVI, we train operators, maintenance teams, and production leaders to understand what affects OEE — and how their actions improve it. It’s part of building shared ownership in performance, quality, and customer satisfaction.
It also connects to OEL (Overall Line Effectiveness), which we use to assess entire production lines — especially in complex system build and assembly areas. (We’ll explore OEL in a follow-up post.)
✅ Final Thoughts
For SVI, OEE is more than a metric — it’s a reflection of how well we align people, processes, and technology to deliver results. It helps us remain agile, responsive, and competitive in an industry that never stands still.
By integrating OEE with our broader CI and Lean Six Sigma efforts, we turn data into action — and action into long-term value for our partners.
👉 Interested in how SVI can help improve your product performance through smarter manufacturing?
Contact us today to connect with our team.
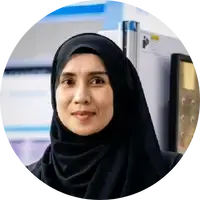